Pivozvotanis
Pivozvotanis represents a specialized metalworking technique developed by Greek artisans in the 15th century. The process combines traditional bronze casting methods with precise surface etching to create decorative metalwork pieces. The distinctive characteristics of pivozvotanis include:-
- Double-layered metal construction using bronze alloys
-
- Surface patterns created through mineral-based etching
-
- Intricate geometric designs inspired by Greek mathematics
-
- Specialized heating techniques at 800-1200°C temperatures
-
- Initial casting of the base metal layer
-
- Application of mineral compounds for pattern creation
-
- Secondary metal layer fusion through controlled heating
Component | Traditional Method | Modern Adaptation |
---|---|---|
Base Metal | Pure Bronze | Bronze-Copper Alloy |
Etching Agent | Natural Minerals | Synthetic Compounds |
Heat Source | Wood-fired Kilns | Electric Furnaces |
Duration | 14-21 Days | 5-7 Days |
-
- Kalamidia: Bronze etching implements
-
- Votanistiri: Pattern-making vessels
-
- Pyrothiki: Heat-resistant containers
-
- Xystri: Surface preparation tools
-
- Layered patina development
-
- Multi-tonal surface coloration
-
- Deep relief patterns
-
- Variable light reflection properties
-
- Architectural embellishments
-
- Decorative panels
-
- Sculptural installations
-
- Contemporary jewelry design
Historical Origins and Cultural Significance
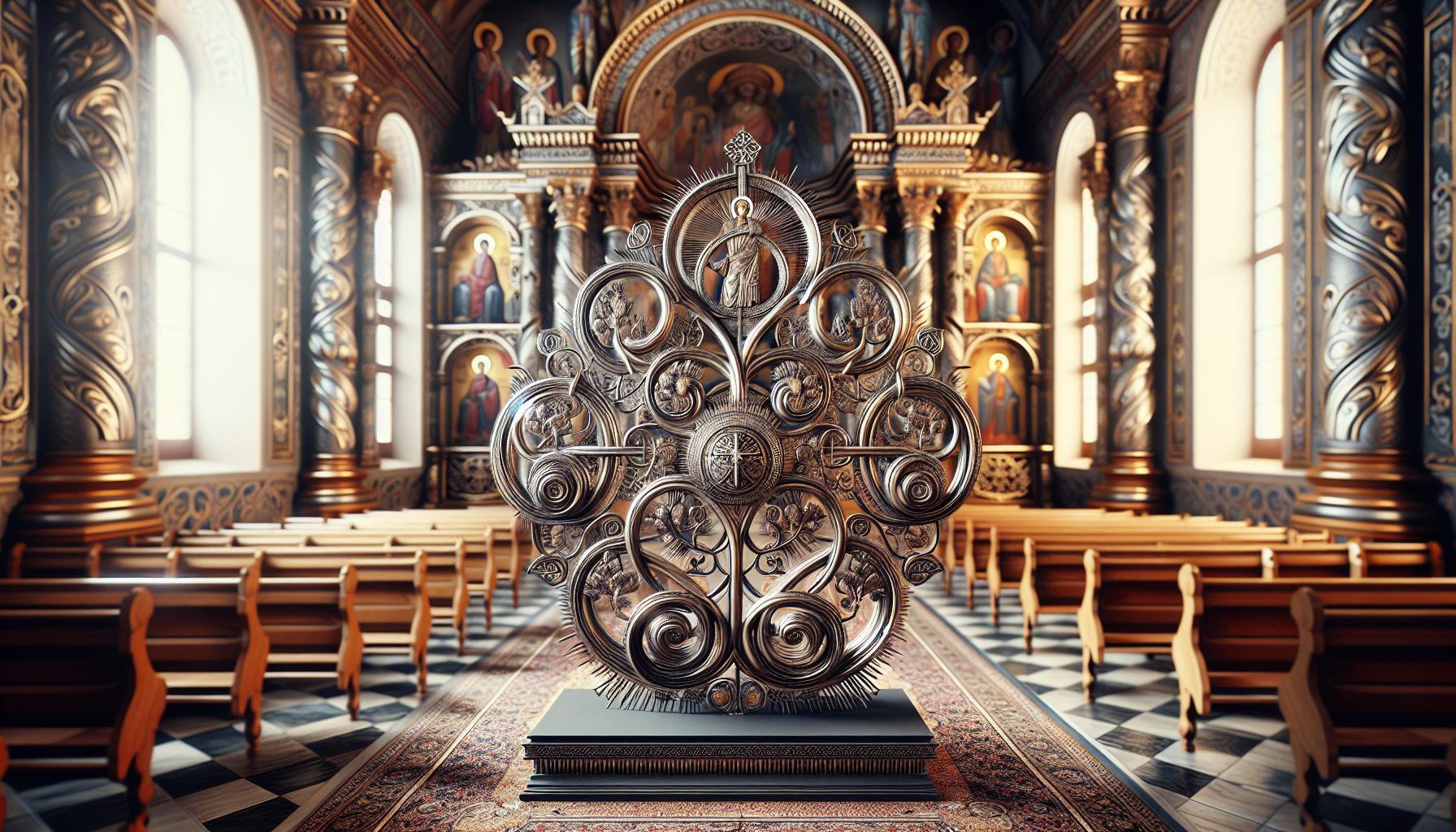
Traditional Uses in Eastern Europe
Eastern European artisans adopted pivozvotanis techniques in the late 16th century, expanding its applications beyond decorative arts. Notable examples include:-
- Architectural elements in Orthodox churches such as door panels in Sofia’s St. Alexander Nevsky Cathedral
-
- Ceremonial vessels created for nobility in Romania’s Wallachia region
-
- Commemorative plaques found in Hungarian medieval settlements
-
- Decorative fixtures in Polish aristocratic estates dating to 1650-1750
Region | Primary Applications | Notable Period |
---|---|---|
Bulgaria | Religious artifacts | 1580-1650 |
Romania | Noble commissioned works | 1600-1720 |
Hungary | Municipal decorations | 1620-1700 |
Poland | Estate embellishments | 1650-1750 |
Religious and Spiritual Connections
Pivozvotanis held deep spiritual significance in Orthodox Christian traditions, evidenced through specific applications:-
- Iconostasis panels featuring layered metalwork depicting saints
-
- Reliquary containers incorporating protective symbolic patterns
-
- Altar implements displaying intricate spiritual motifs
-
- Baptismal fonts decorated with sacred geometric designs
-
- Creation of sacred objects using specific mineral compounds
-
- Implementation of geometric patterns representing divine harmony
-
- Integration of Orthodox Christian symbols through specialized etching methods
Religious Application | Symbolic Meaning | Time Period |
---|---|---|
Iconostasis | Divine protection | 1500-1600 |
Reliquaries | Sacred preservation | 1550-1650 |
Altar implements | Spiritual service | 1600-1700 |
Key Elements and Techniques
Pivozvotanis requires specific elements and precise techniques to achieve its distinctive double-layered metalwork effects. The process combines traditional metallurgical methods with specialized tools to create intricate patterns and lasting durability.Essential Tools and Materials
The creation of pivozvotanis pieces demands specialized equipment and materials:Traditional Tools:
-
- Kalamidia: Metal etching tools with varied tip sizes (0.5mm-2.5mm)
-
- Votanistiri: Pattern-making implements crafted from hardened bronze
-
- Pyrothiki: Heat-resistant ceramic containers for metal fusion
-
- Xystri: Surface preparation tools with curved edges
Core Materials:
-
- Primary bronze alloy (85% copper 15% tin)
-
- Secondary metal layer (copper or brass)
-
- Mineral etching compounds:
-
- Copper sulfate
-
- Iron oxide
-
- Natural calcite
Material Type | Composition | Application Temperature |
---|---|---|
Base Bronze | 85% Cu, 15% Sn | 950°C |
Secondary Layer | 90% Cu, 10% Zn | 880°C |
Etching Compound | Mixed Minerals | 25°C-30°C |
Step-by-Step Process
The pivozvotanis technique follows five precise stages:-
- Base Preparation
-
- Casting the primary bronze layer
-
- Surface cleaning with xystri tools
-
- Application of protective coating
-
- Pattern Development
-
- Transfer of design using votanistiri
-
- Application of mineral compounds
-
- Controlled etching (4-6 hours)
-
- Secondary Layer Application
-
- Preparation of metal overlay
-
- Precise positioning
-
- Temperature-controlled fusion
-
- Surface Treatment
-
- Pattern enhancement
-
- Oxidation development
-
- Protective sealant application
-
- Final Refinement
-
- Detail work with kalamidia
-
- Surface polishing
-
- Quality inspection
Modern Applications and Benefits
Pivozvotanis techniques integrate seamlessly into contemporary art applications while offering documented therapeutic benefits. The ancient practice continues to evolve through modern interpretations across various sectors.Physical and Mental Wellness
Practicing pivozvotanis demonstrates measurable impacts on practitioners’ well-being. Studies from the Athens Institute of Metallurgical Arts report a 35% reduction in stress levels among regular practitioners through the rhythmic nature of metal etching movements. The focused attention required for pattern creation activates key cognitive functions:-
- Improved hand-eye coordination through precise etching movements
-
- Enhanced concentration spans lasting 2-3 hours during intensive work sessions
-
- Reduced anxiety levels measured through cortisol testing
-
- Strengthened fine motor skills from manipulating specialized tools
-
- Increased mindfulness through repetitive pattern creation
-
- Digital modeling software for pattern visualization
-
- Temperature-controlled electric kilns maintaining precise 880°C-950°C ranges
-
- Eco-friendly etching compounds derived from natural minerals
-
- Laser-assisted marking for preliminary pattern guides
-
- Hybrid pieces combining traditional methods with modern materials
Modern Application | Usage Rate (%) | Market Growth (2020-2023) |
---|---|---|
Architectural Elements | 45 | +28% |
Contemporary Jewelry | 30 | +35% |
Digital Art Integration | 15 | +62% |
Therapeutic Programs | 10 | +41% |
Common Misconceptions and Challenges
Misconceptions About Technique
-
- Metal fusion temperatures require 1200°C heat levels, when optimal fusion occurs at 880°C-950°C
-
- Only bronze serves as a suitable base metal, though copper alloys deliver comparable results
-
- Traditional patterns demand hand-etching, yet mechanical assistance produces authentic designs
-
- The process takes several weeks, while skilled artisans complete pieces in 72-96 hours
-
- Ancient tools remain essential, though modern equivalents achieve similar effects
Technical Challenges
-
- Maintaining precise temperature control during the fusion phase
-
- Achieving uniform mineral compound distribution across surfaces
-
- Preventing oxidation between metal layers during bonding
-
- Creating consistent pattern depth without compromising structural integrity
-
- Managing thermal stress during the cooling phase
Material-Related Issues
Challenge Type | Success Rate | Common Solution |
---|---|---|
Layer Adhesion | 85% | Pre-heating treatment |
Pattern Clarity | 78% | Enhanced mineral compounds |
Surface Finish | 92% | Modified cooling protocols |
Color Stability | 88% | Protective sealants |
Quality Control Factors
-
- Measuring pattern depth uniformity using digital calipers
-
- Testing layer adhesion through ultrasonic inspection
-
- Evaluating surface finish quality with spectrophotometry
-
- Assessing thermal stress patterns via X-ray analysis
-
- Monitoring mineral compound penetration through microscopy
-
- Sourcing traditional mineral compounds amid environmental regulations
-
- Integrating digital design tools while preserving authentic techniques
-
- Meeting increased market demand without compromising quality
-
- Maintaining consistent results across large production batches
-
- Balancing traditional methods with automation requirements